Technologies for air protection and reduction of VOC emissions
We supply all standard types of VOC abatement technologies. The selection of the appropriate technology and its design is carried out with regard to investment and operating costs, according to the customer’s requirements. All offered technologies are delivered on a turnkey basis, including warranty and post-warranty service.
Do you have any questions or would you like to cooperate with us?
Write to us and we will get back to you.
THE PROCESS OF ACQUIRING AIR PROTECTION TECHNOLOGY
The need to address pollutant emissions arises most often for the following reasons:
- Conflicts with applicable air protection legislation (existing production or investment project)
- Existence of a physically or morally obsolete or non-functional existing emission treatment system
- Evaluation of the possibility of replacing an inefficient, usually not economically viable solution with a new technology
If this situation concerns you, please contact us.
Our experts will be happy to assist you and together guide you through all the necessary steps.
A well-defined demand is one of the determining conditions for developing an optimal solution.
This often underestimated step has a major impact on the quality of the subsequent technical design.
Our company has one of the largest and best-equipped emission measurement groups and, with the support of our own physico-chemical laboratory, we carry out pollutant emission measurements tailored to the needs of the technical solution.
A well-defined demand is one of the determining conditions for developing an optimal solution.
This often underestimated step has a major impact on the quality of the subsequent technical design.
Our company has one of the largest and best-equipped emission measurement groups and, with the support of our own physico-chemical laboratory, we carry out pollutant emission measurements tailored to the needs of the technical solution.
The usual scope of documentation is production documentation of mechanical, electrical, MaR, construction (if it is current and required). In case of need and interest, we also provide documentation for building permits (including their processing).
The usual scope of documentation is production documentation of mechanical, electrical, MaR, construction (if it is current and required). In case of need and interest, we also provide documentation for building permits (including their processing).
The equipment is supplied and installed as a turnkey delivery by our own staff, who also provide training in the operation and maintenance of the technology.
The commissioning process comprises individual tests, comprehensive tests, commissioning of the test plant and then commissioning for permanent operation. This is completed with a guarantee measurement and the handover of the complete technical documentation.
The standard warranty is 24 months. Based on service contracts, we offer unlimited after-sales service for the entire lifetime of the equipment. This includes regular annual maintenance and preventive maintenance.
For operational service interventions, we equip the equipment with remote management, which minimizes the need for travel and significantly reduces service costs.
All servicing is provided by our own staff.
THE PROCESS OF ACQUIRING AIR PROTECTION TECHNOLOGY
- NEED
- DEMAND
- TECHNICAL PROPOSAL, QUOTATION
- PROJECTION
- PRODUCTION OF EQUIPMENT
- INSTALLATION
- COMMISSIONING
- SERVICE
The need to address pollutant emissions arises most often for the following reasons:
- Conflicts with applicable air protection legislation (existing production or investment project)
- Existence of a physically or morally obsolete or non-functional existing emission treatment system
- Evaluation of the possibility of replacing an inefficient, usually not economically viable solution with a new technology
If this situation concerns you, please contact us.
Our experts will be happy to assist you and together guide you through all the necessary steps.
A well-defined demand is one of the determining conditions for developing an optimal solution.
This often underestimated step has a major impact on the quality of the subsequent technical design.
Our company has one of the largest and best-equipped emission measurement groups and, with the support of our own physico-chemical laboratory, we carry out pollutant emission measurements tailored to the needs of the technical solution.
The result of this step is the elaboration of a proposal for an optimal solution according to the investor’s priorities (Capex/Opex, etc.), or the elaboration of solution variants for the subsequent process of selecting the technology and its supplier. It includes a price calculation prepared according to the needs and layout of the investor.
The usual scope of documentation is production documentation of mechanical, electrical, MaR, construction (if it is current and required). In case of need and interest, we also provide documentation for building permits (including their processing).
The production of the equipment is mostly carried out in the Czech Republic. Our products are supplied to domestic customers as well as abroad and are manufactured in accordance with the applicable European regulations and technical standards.
The equipment is supplied and installed as a turnkey delivery by our own staff, who also provide training in the operation and maintenance of the technology.
The commissioning process comprises individual tests, comprehensive tests, commissioning of the test plant and then commissioning for permanent operation. This is completed with a guarantee measurement and the handover of the complete technical documentation.
The standard warranty is 24 months. Based on service contracts, we offer unlimited after-sales service for the entire lifetime of the equipment. This includes regular annual maintenance and preventive maintenance.
For operational service interventions, we equip the equipment with remote management, which minimizes the need for travel and significantly reduces service costs.
All servicing is provided by our own staff.
TYPES OF VOC ABATEMENT TECHNOLOGIES
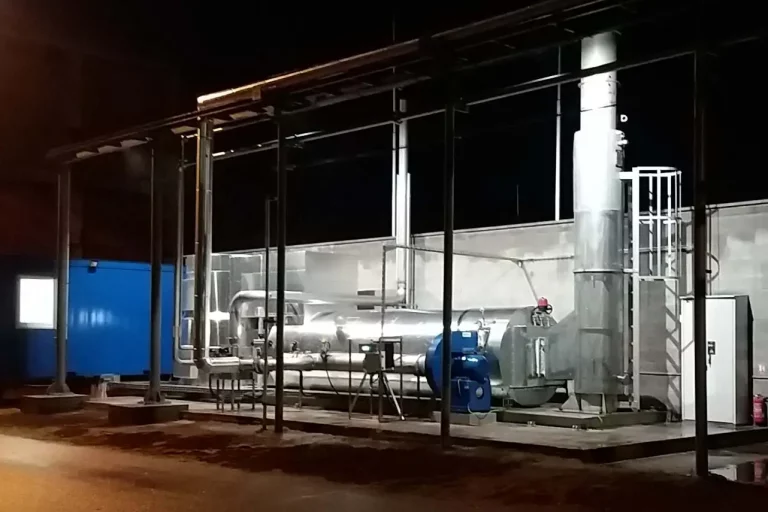
Recuperative catalytic oxidation (KNV, KOJ)
A technologically simple system for cleaning organic emissions by combustion on a catalyst bed.
The system is designed for medium and higher VOC concentrations in emissions (2 - 6 g/m3)
The basic elements of the technology are a heat exchanger, a heating chamber (heated by electricity or gas) for heating the polluted air and a reactor with a catalytic charge.
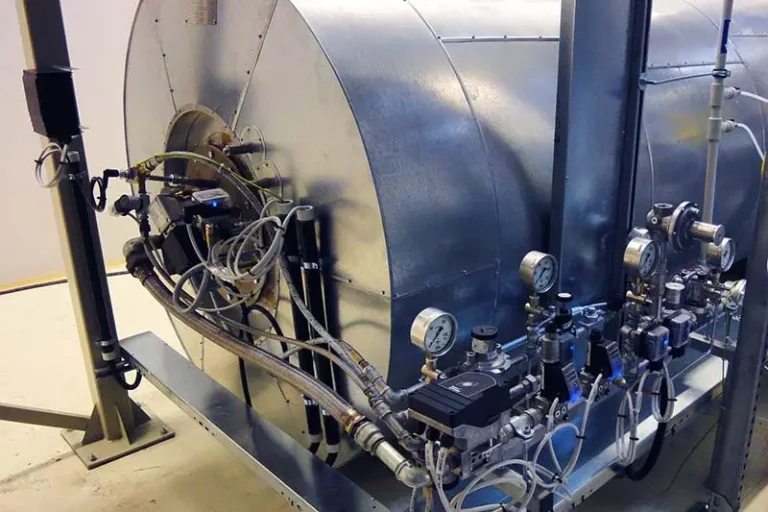
Recuperative thermal oxidation (TNV)
Technology for cleaning organic emissions by thermal combustion.
The system is used for higher concentrations of VOCs in emissions (3-10g/m3), especially where the heat generated can be subsequently used.
The technology consists of a central combustion chamber with a gas burner integrated into a circular flue gas heat exchanger.
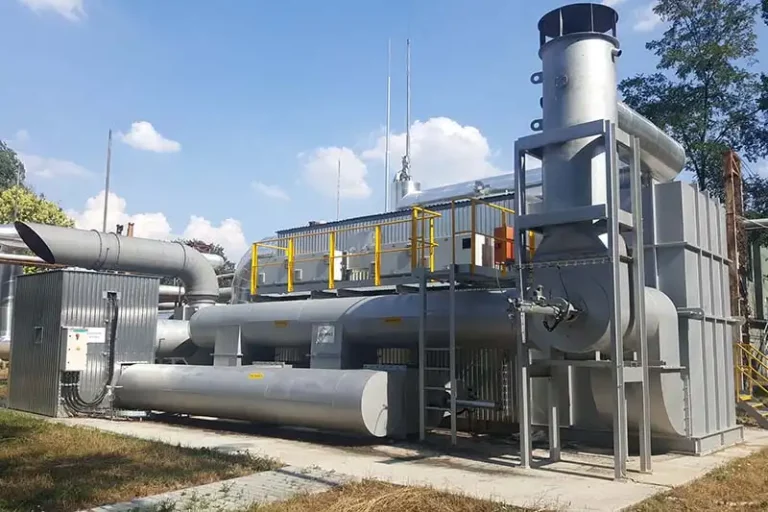
Regenerative catalytic oxidation (RCO, RKNV)
A sophisticated system for very energy-efficient cleaning of organic emissions in catalytic reactors.
The system is designed for low and medium concentrations of VOC in emissions (0.2 - 3g/m3)
The basic elements of the technology are interconnected chambers (reactors) with a heat exchanged ceramic liner, an emissions heating area (electricity or gas) and a catalytic reaction bed.
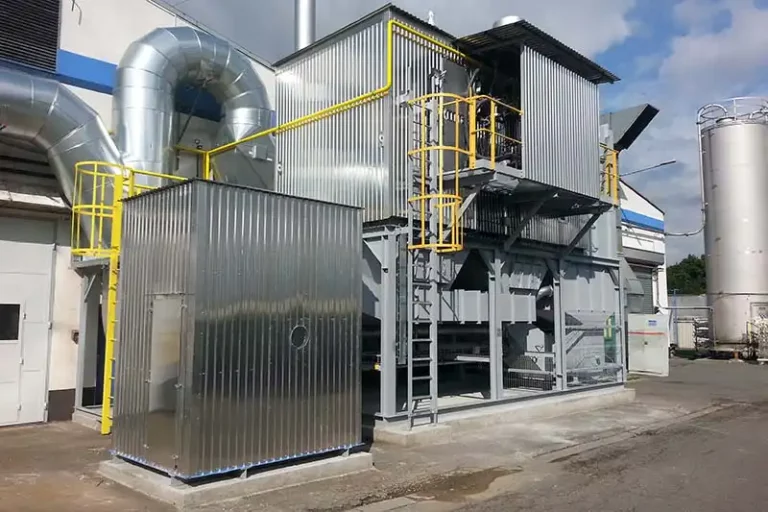
Regenerative Thermal Oxidation (RTO, RTNV)
Energy-saving system for cleaning organic emissions by thermal combustion.
The system is designed for medium VOC concentrations in emissions (1.5 - 5g/m3).
The technology usually consists of 2 - 3 chambers with heat exchanged ceramic filling and a connecting combustion chamber with a gas burner.
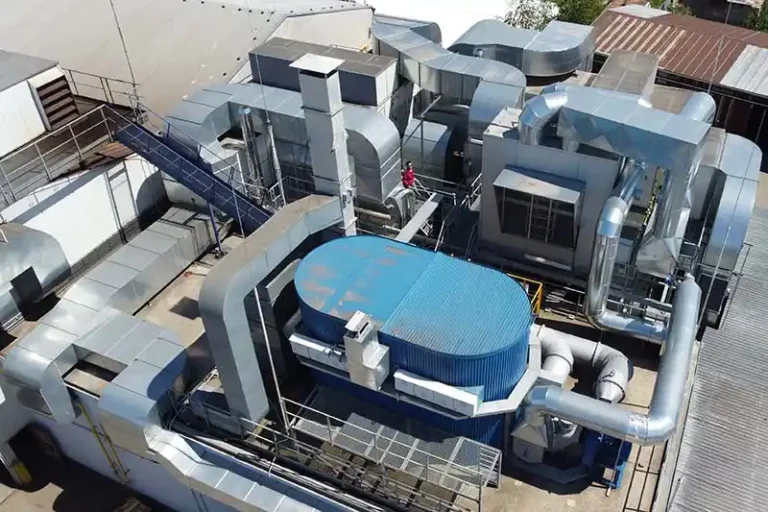
Zeolite rotating concentrator
A system for concentrating very low levels of organic pollution from high volumes of treated emissions.
The system is designed for low concentrations of VOC in emissions (0.1 - 0.5 g/m3) in high air volumes (tens to hundreds of thousands m3/h).
The technology consists of a zeolite concentrator and a downstream oxidation end-effector, which can be TNV, RTO, and RCO.